Industrial steel buildings have become a hallmark of modern construction, offering an ideal blend of durability, flexibility, and economic efficiency. With a noticeable versatility in applications spanning warehouses, factories, and even commercial complexes, these structures are unmatched in their ability to provide expansive, unobstructed interior space. One crucial element that often becomes the focal point for businesses considering these buildings is their price. Understanding the various factors affecting the cost can empower decision-makers with the knowledge to make informed choices that align with both their budgetary constraints and operational needs.
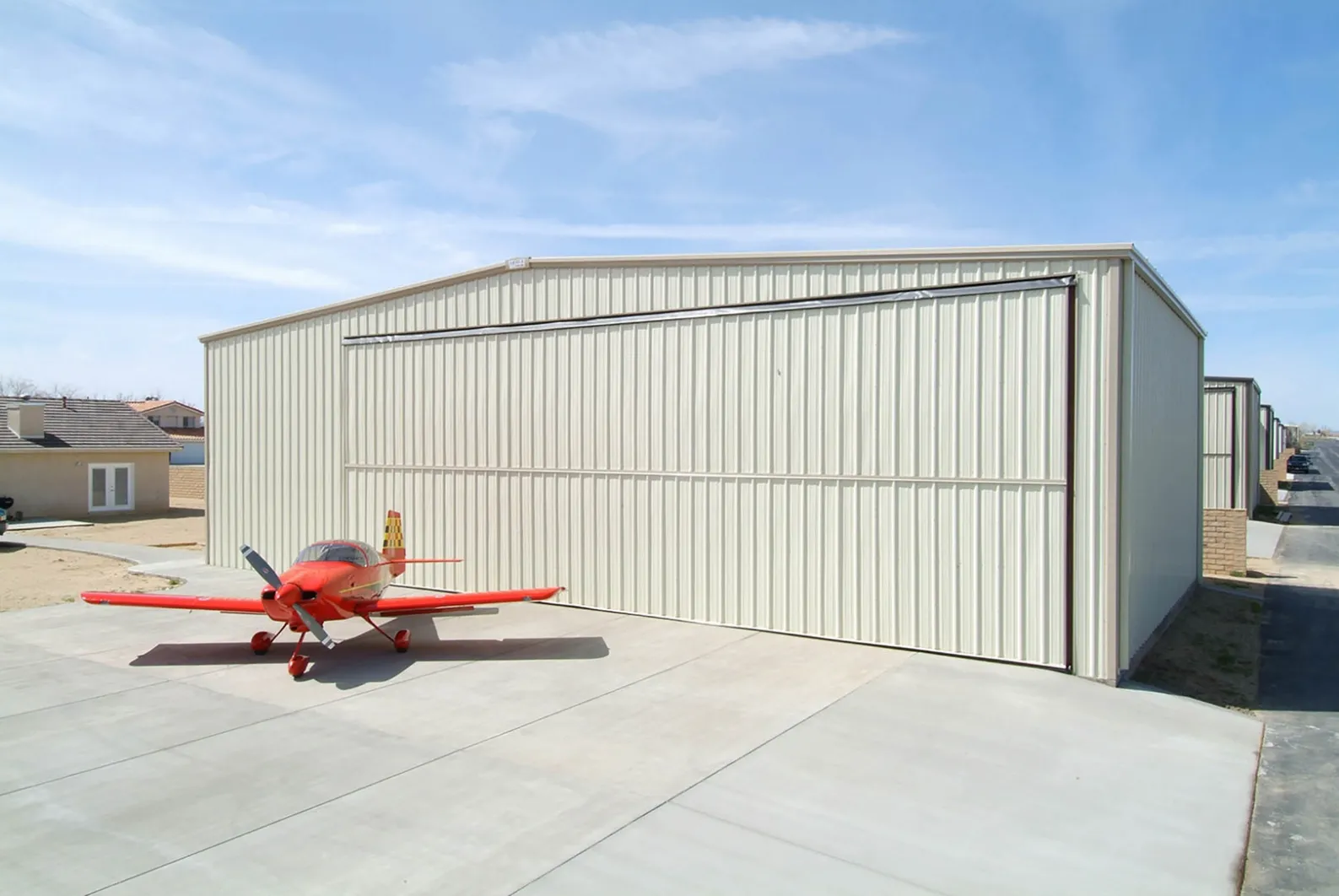
Steel buildings are reputed for their cost-effectiveness, yet the notion of price extends beyond a simple dollar value. The cost is a composite of multiple layers, including material costs, design customization, labor, and even operational longevity. For instance, while the initial investment might be higher than traditional wooden structures, the longevity and minimal maintenance of steel often make it more economical over time. Expert analyses suggest that the initial material costs generally account for about 50% of the total expenditure. This includes high-quality steel, coatings, and other elements that ensure the building’s resilience against environmental factors like corrosion and extreme weather.
Customization dramatically influences pricing as it tailors the building to specific needs—whether that involves specific dimensions, unique architectural designs, or additional facilities. Naturally, these preferences translate into varying costs due to the need for specialized manufacturing and the use of premium materials. A trusted approach for businesses is to outline essential features and identify optional ones that could be incorporated at a later stage, thereby optimizing the initial outlay.
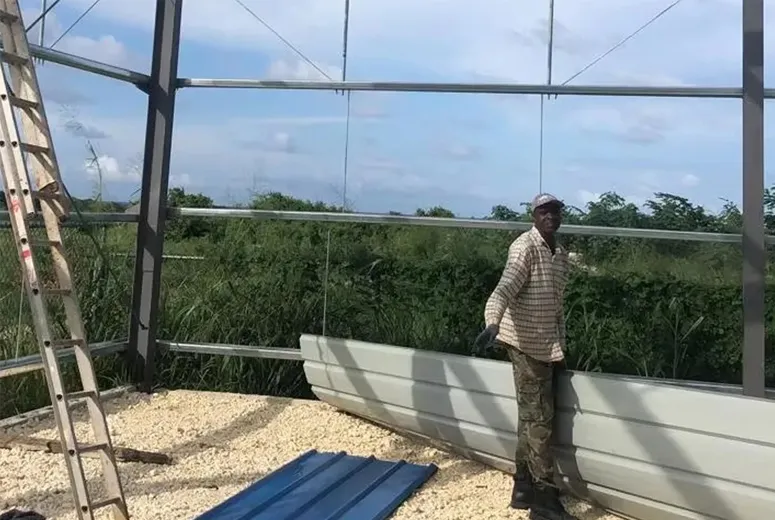
Labor costs also play a decisive role. Unlike conventional buildings, steel structures often require specialized construction crews with expertise in handling and assembling pre-fabricated components. Although these teams might come with a higher hourly rate, their proficiency typically reduces overall construction time, hence saving costs associated with prolonged project timelines. In regions where skilled labor is in abundance, companies may find a strategic advantage, potentially contracting locally for more competitive pricing without compromising on quality.
Furthermore, location is often an underrated yet pivotal factor in the cost structure. Transporting materials can be a significant expense if the manufacturing plant is situated far away from the construction site. Ordering from manufacturers with facilities closer to the desired location can mitigate this issue. The regulatory environment should also be considered, as areas with strict zoning laws or requirements can increase the cost due to necessary compliance modifications and certifications.
industrial steel buildings prices
Financial planning for industrial steel buildings must accommodate both direct and indirect costs. Indirect costs include potential taxation, insurance, land acquisition, and energy consumption, which should be calculated in advance to avoid budget overruns. Buildings designed with energy efficiency in mind can end up saving on operational costs, even if they require a higher initial investment due to advanced insulation or solar energy systems.
Many industry experts advise using cost-benefit analysis to assess potential return on investment (ROI) associated with steel buildings. This analysis encompasses both tangible financial returns and intangible benefits such as enhanced efficiency, employee satisfaction, and brand strength derived from environmentally friendly practices. As steel is a 100% recyclable material, buildings that opt for this resource contribute positively to sustainability goals, often enhancing brand reputation which can indirectly affect profitability.
In gauging the competitive landscape, knowing where your investment in steel buildings compares with competitor spending can be pivotal. Understanding these dynamics offers a unique vantage point from which businesses can strategically plan their investments to remain or become industry leaders.
Choosing the right vendor or manufacturer is paramount. Engaging a supplier with a robust track record ensures reliability, quality, and adherence to delivery timelines. Many businesses find value in testimonials and case studies or, better yet, visiting existing sites to witness firsthand the built quality and performance over a period. Such direct experience acts as a compelling factor in building trust and validating the investment.
In conclusion, the pricing of industrial steel buildings is a complex art of integrating immediate material costs, long-term financial strategy, and operational efficiency. Decision-makers are encouraged to approach the process with a comprehensive understanding of the building’s purpose, allocate budgetary provisions that account for potential future expansions or modifications, and cultivate partnerships with reputable suppliers who can offer guidance and insight throughout the project lifecycle. Emphasizing these elements ensures the investment not only aligns with current needs but is adaptable and scalable for future challenges and advancements in the industry.