Evaluating the cost of a 200 x 400 steel building requires a nuanced understanding of various influencing factors. Steel buildings have surged in popularity due to their durability, flexibility, and cost-effectiveness for large-scale constructions. However, the price of erecting such a massive structure isn't merely a multiplication of its square footage. To achieve a comprehensive understanding, one must consider all variables, ensuring a structured financial plan that aligns with specific project needs.
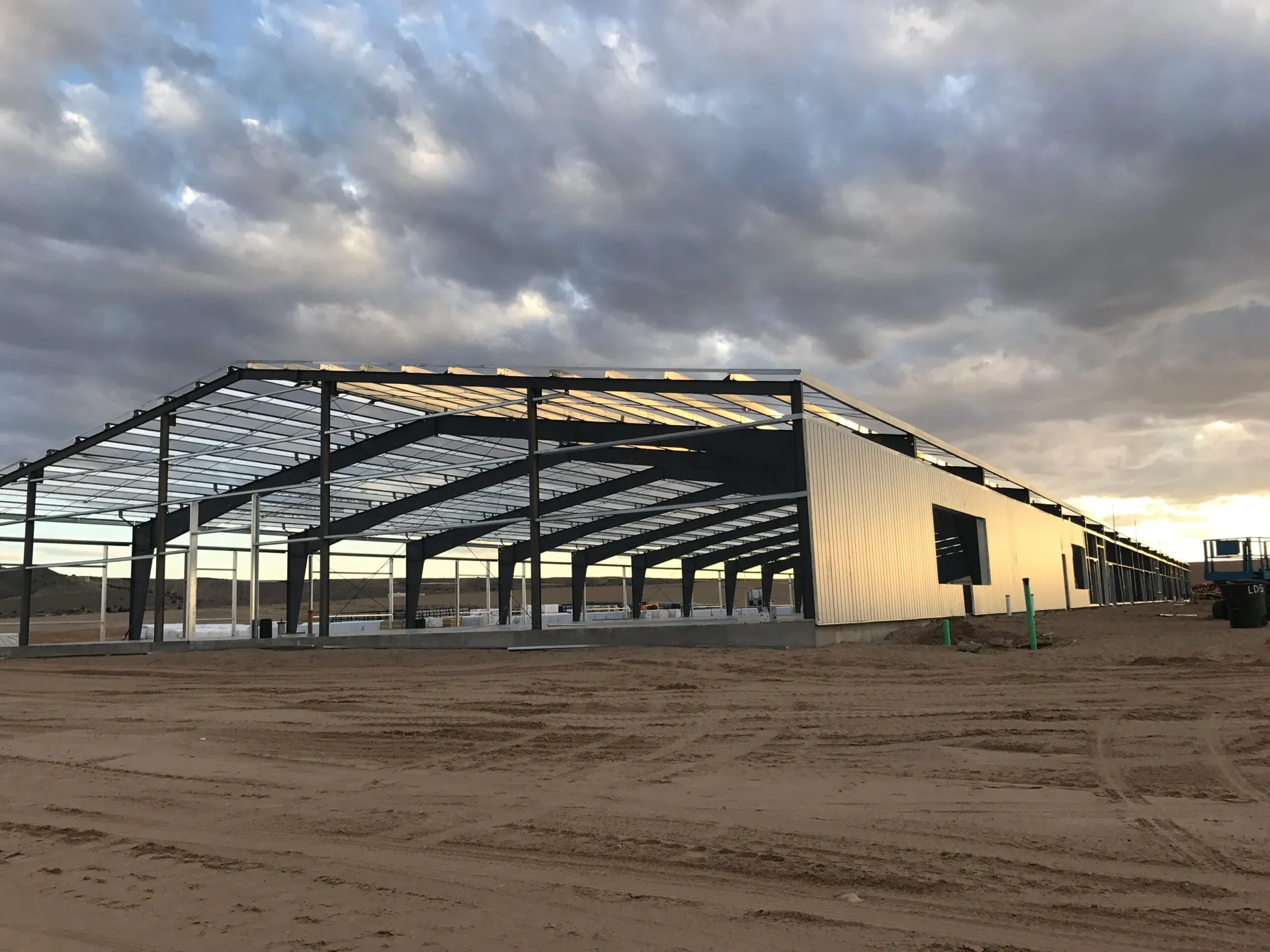
Firstly, the location of your construction site plays a pivotal role. Geographic location affects the labor costs, building codes, and even the cost of materials delivered to your site. For instance, constructing in an urban area might lead to higher labor costs due to higher living expenses, whereas rural areas might contend with increased transportation costs for materials. Additionally, local climate can impact the insulation and weatherproofing requirements, further influencing the budget.
The design complexities of the steel building cannot be overstated. A basic, simple design will always be more cost-effective than a customized architecture featuring unique aesthetic elements. Features like mezzanines, multi-level staircases, or customized facades amplify the structural intricacy and, consequently, the overall cost. It's crucial to balance between aesthetic requirements and functional needs without compromising the budget.
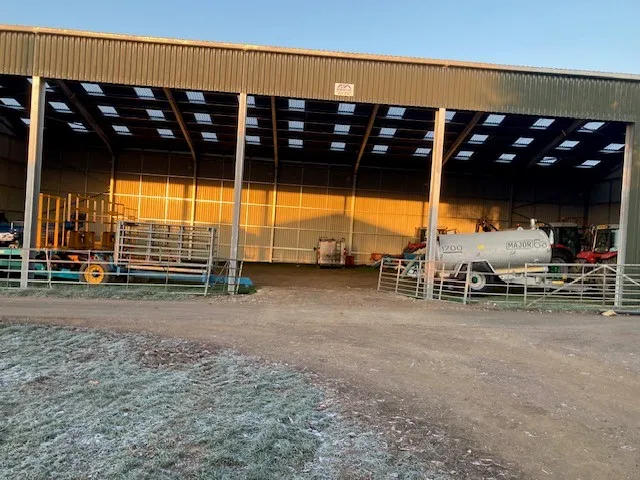
Material costs, primarily the steel itself, have a direct impact on the project's financial outlay. Steel prices fluctuate based on global market dynamics. Tariffs, international trade agreements, and even geopolitical tensions can affect prices. Engaging in thorough market research or consulting with industry experts can provide insights into when to purchase materials to capitalize on the best prices. Additionally, consider the grade and quality of the steel; higher-grade materials can ensure longevity and reduce future maintenance costs.
Speaking of expertise, choosing the right contractor is vital for both budget adherence and quality assurance. Experienced contractors not only streamline the construction process but also mitigate unforeseen expenses through their understanding of potential challenges and solutions. Expertise comes at a price, though—it is advisable to vet contractors thoroughly, evaluating past work, client testimonials, and industry reputation before finalizing your decision.
200 x 400 steel building cost
Regulatory requirements, including permits and inspections, must not be overlooked. Depending on the jurisdiction, these costs can vary significantly and typically include a mix of building permits, environmental impact assessments, and safety inspections post-construction. Navigating these bureaucratic requirements efficiently requires hiring professionals familiar with local building codes and regulations, which although an added upfront cost, saves potential legal troubles and fines later.
Maintenance also factors into the overall cost although it materializes post-construction. A high-quality steel building that adheres to industry standards will require minimal maintenance, yet it's essential to budget for periodic inspections and occasional repairs. Weather conditions such as intense heat, humidity, or heavy snowfall dictate maintenance needs, impacting the annual upkeep budget.
There's also the 'opportunity cost' to consider—delays in the construction timeline can lead to financial penalties or lost revenue opportunities if the building is intended for commercial use. Ensuring efficient project management and adhering to timelines is paramount for budget control. Opting for prefabricated components can expedite the process, allowing for faster assembly and reduced labor costs. However, this decision should weigh the pros of speed and cost against potential compromises in customization and site-specific adaptations.
For a definitive and tailored cost assessment, employing the services of a cost estimator or builder with a proven track record in large-scale steel constructions is advisable. They provide detailed cost breakdowns and forecasts, helping stakeholders make informed decisions based on refined cost data rather than estimations. Trust in the execution process is enhanced through transparency and accountability—qualities essential for successful project delivery.
In conclusion, the cost of a 200 x 400 steel building can’t be pinned to a single figure due to its intrinsic dependency on location, design, material quality, contractor expertise, and regulatory adherence. A strategic, informed approach that incorporates thorough research, detailed planning, and expert guidance will not only optimize initial expenditure but also safeguard against future financial strain, ensuring a sustainable investment.