In the contemporary landscape of commercial real estate and industrial storage solutions, prefab warehouse construction has emerged as a significant shift. Prefabricated warehouses not only offer a cost-efficient solution but also ensure rapid deployment with a remarkable level of architectural integrity. Understanding the intricacies of prefab warehouse prices can give businesses a competitive edge while fulfilling storage and distribution needs effectively.
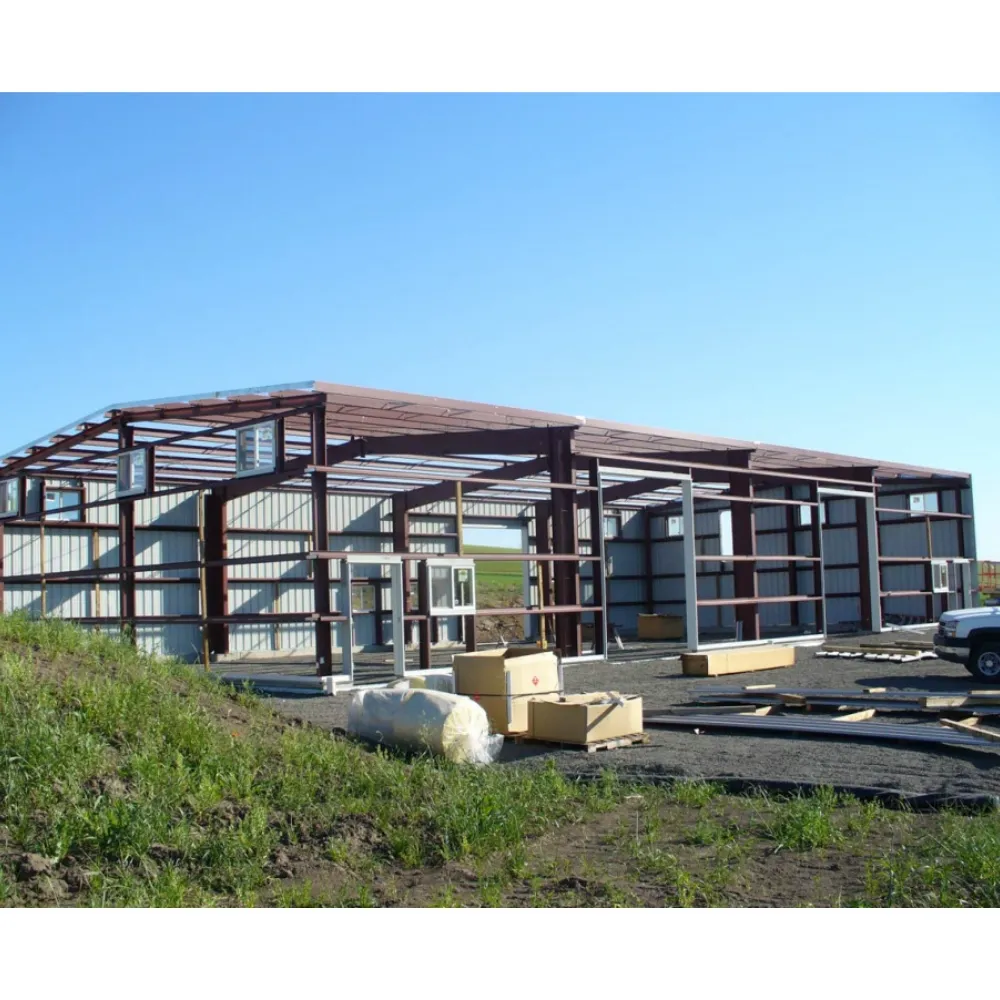
Navigating through the broad spectrum of prefab warehouse pricing necessitates an understanding of several critical factors. Primarily, the cost implications hinge on the materials used, size of the structure, geographical location, customization, and the complexity of the project. Unlike traditional construction which can be plagued by delays and cost overruns, prefab warehouses present a well-defined budget and timeline.
The foundation of any prefab warehouse is its material composition. Typically, steel is the material of choice due to its durability, flexibility, and sustainability. Steel structure prices can vary; however, they are generally lower per square foot compared to traditional construction materials, offering excellent value for money. Furthermore, savings are amplified by the reduction in construction time, as prefab components are manufactured offsite and quickly assembled onsite.
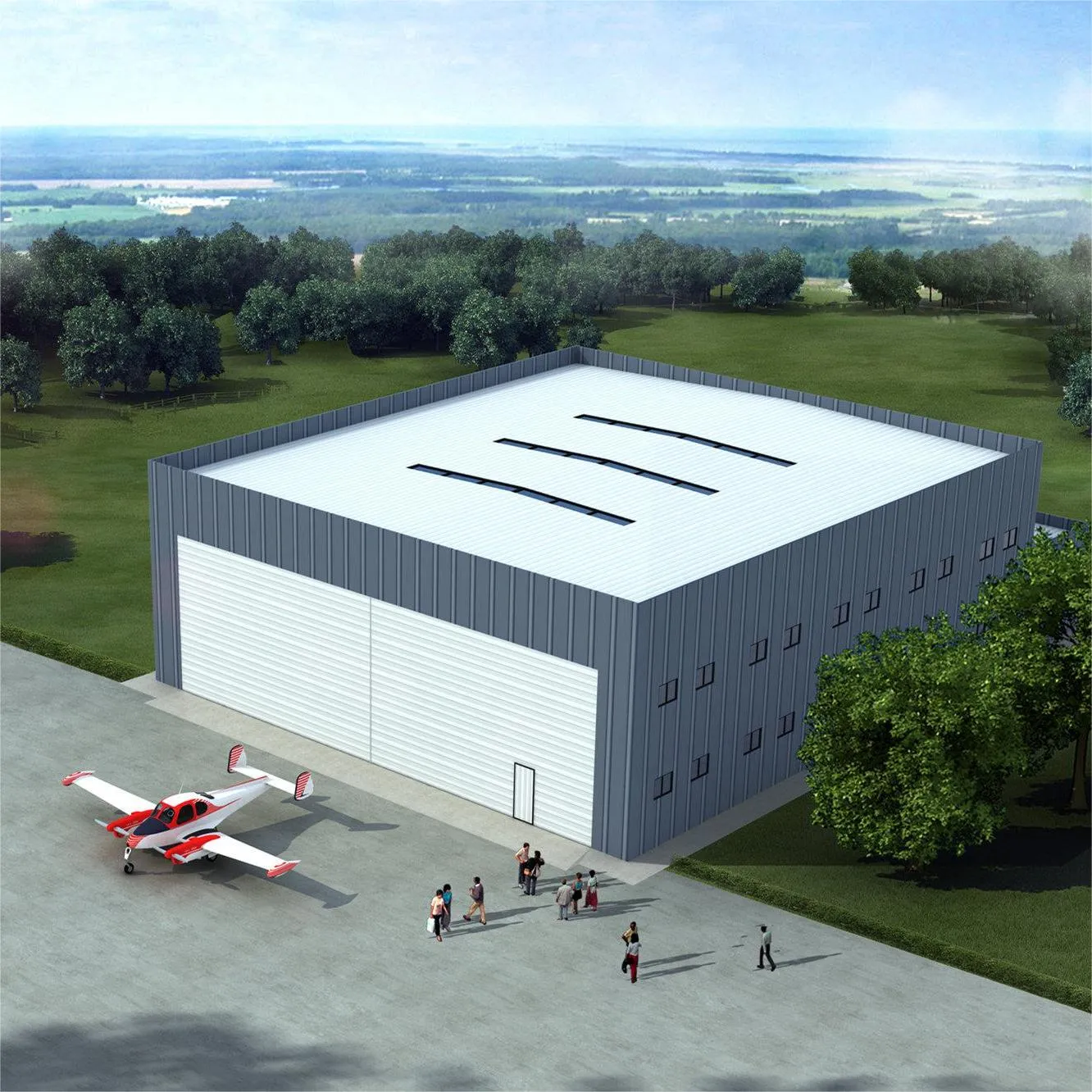
Size plays a crucial role in determining the price of a prefab warehouse. Larger warehouses require more materials, labor, and site preparation, which increases the initial investment. However, economies of scale generally apply as the warehouse size increases, the cost per square foot often declines, translating to greater efficiency for large-scale operations.
Geographical location affects prefab warehouse costs significantly. Prices are influenced by local regulations, labor costs, and site accessibility. In metropolitan areas, demand for warehouse space can drive up costs, while rural areas might offer savings due to lower land and labor costs. Additionally, proximity to key transportation hubs such as ports or rail networks can make certain locations more desirable, thereby influencing the overall price.
Customization is another key factor influencing the cost. Businesses may require specific features such as enhanced insulation, climate control systems, or specialized loading docks. Each of these requirements can increase the initial costs but may offer long-term savings or efficiency gains depending on operational needs. Therefore, assessing the balance between customization costs and potential efficiencies is crucial.
prefab warehouse prices
The complexity of the project can impact the overall cost structure. Simple, rectangular designs are more cost-effective than complex structures with multiple levels or unconventional architecture. While unique designs may serve aesthetic or functional purposes, they can escalate both material and labor costs significantly.
Professional expertise is paramount to managing prefab warehouse projects efficiently. Engaging with experienced architects, engineers, and contractors can mitigate risks, ensuring that the project is completed within budget and to specification. Expert insight can also provide realistic cost assessments and uncover potential savings that might not be apparent to less experienced project managers.
Trustworthiness in partnership with suppliers and contractors cannot be understated. Selecting reliable partners not only ensures quality materials and workmanship but also delivers the warehouse project within stipulated timelines. Trust is established when suppliers and contractors have a history of successful project completions, high client ratings, and adherence to industry standards.
The authority of suppliers can be measured by their industry recognition and ability to provide bespoke solutions tailored to a client's specific needs. Those with a well-documented history of successful projects and innovative approaches are often best placed to offer authoritative advice and solutions.
Finally, businesses must consider the long-term cost implications of prefab warehouse investments. While initial costs are important, ongoing operational efficiencies and resilience to future business demands can justify a higher initial outlay. Prefab warehouses offer flexibility for expansion, relocation, and adaptation to new business strategies, ensuring that they remain a viable investment in the rapidly changing economic landscape.
In summary, navigating prefab warehouse prices requires a strategic approach informed by a keen understanding of materials, size, location, customization, and project complexity. Through leveraging professional expertise and cultivating trustworthy partnerships, businesses can unlock the full potential of prefabricated solutions, achieving cost-effective and flexible warehousing solutions tailored to their needs.