Understanding the Prefab Warehouse Cost Insights and Expertise
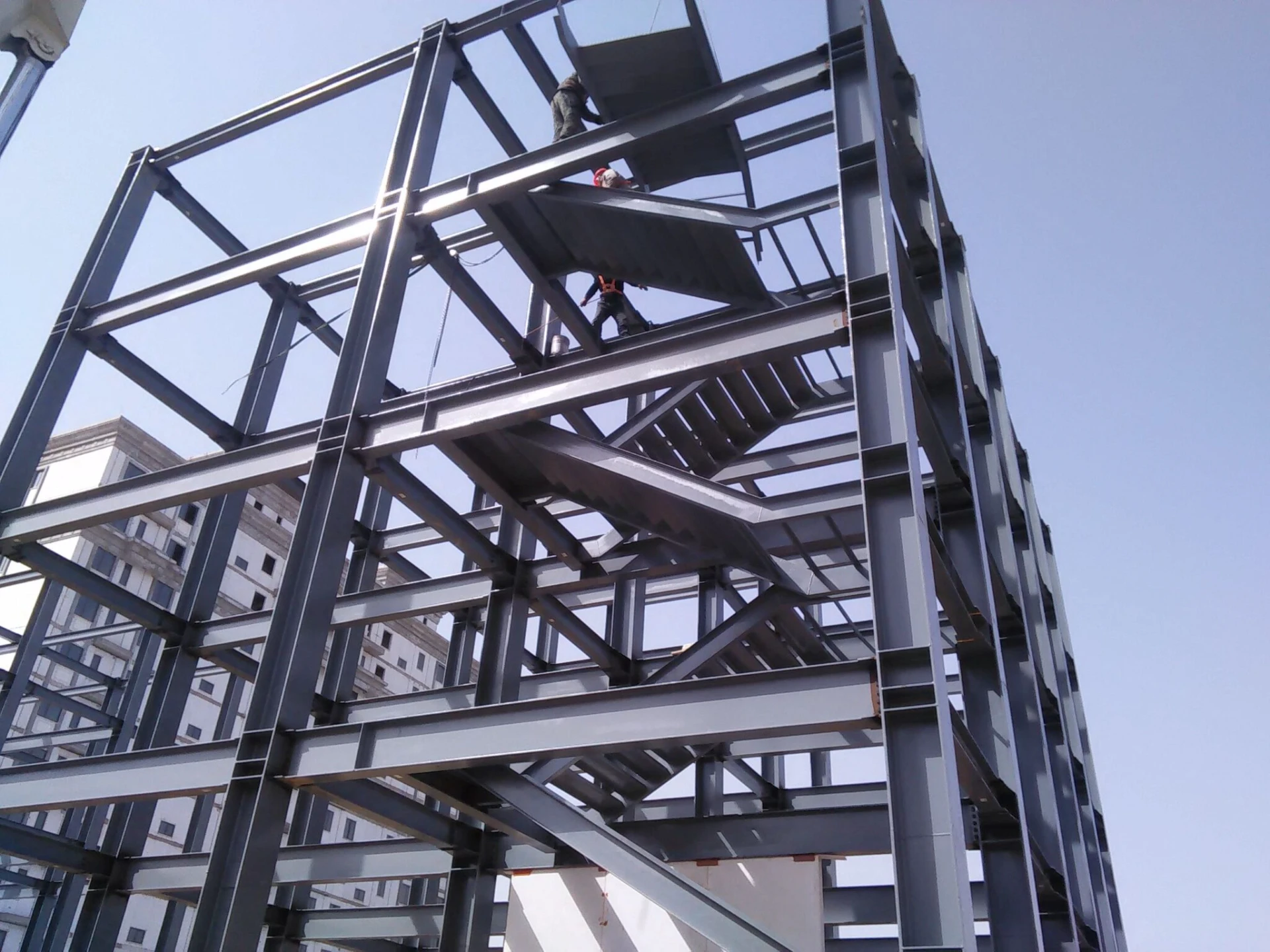
In the rapidly evolving landscape of industrial storage solutions, prefab warehouses have emerged as a crucial and cost-effective option for businesses of all sizes. As companies strive for efficiency and scalability, understanding the cost dynamics of prefab warehouses is pivotal. Here, we delve into the intricacies of prefab warehouse costs, sharing insights from industry experts and highlighting key considerations that can impact the final expenditure.
The Growing Trend
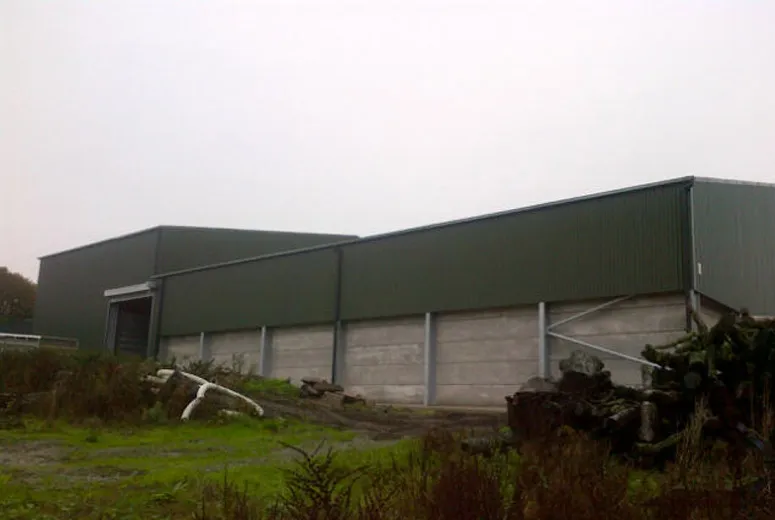
The demand for prefab warehouses has surged in recent years, driven by their flexibility, reduced construction time, and cost-effectiveness. Unlike traditional construction methods, prefab warehouses are manufactured off-site in modules, which are then transported and assembled on location. This approach not only minimizes on-site labor costs but also reduces the potential for project delays due to adverse weather conditions.
Factors Influencing Prefab Warehouse Cost
1. Design Complexity and Size
The complexity and scale of a prefab warehouse significantly influence its cost. A simple design with minimal customization tends to be more affordable, whereas intricate designs with bespoke features can drive up expenses. Size also plays a critical role; larger warehouses require more materials and labor, leading to higher costs. However, economies of scale can sometimes offer cost advantages for larger projects.
2. Materials Used
The choice of materials is another critical factor. Steel, a popular material for prefab warehouses, offers durability and strength but can vary in price based on market fluctuations. Other materials, such as wood or aluminum, provide different benefits and cost structures. Opting for high-quality materials can enhance the longevity and performance of the warehouse, potentially offsetting upfront costs with reduced maintenance expenses over time.
3. Location and Logistics
Transportation and logistical considerations can add to the overall cost. The distance from the manufacturing facility to the assembly site affects the transportation expenses. Additionally, site-specific factors such as ground conditions and local regulations can influence the cost, necessitating thorough site assessments and planning.
prefab warehouse cost
Benefits Outweighing the Costs
Despite the costs associated with prefab warehouses, their benefits often justify the investment. Rapid construction time leads to faster operational readiness, offering companies a competitive edge. Additionally, prefab warehouses can be easily expanded or modified, allowing businesses to adapt to changing needs without significant reinvestment.
Industry Insights
According to industry experts, businesses should approach prefab warehouse investments with a strategic mindset. Conducting a comprehensive cost-benefit analysis is essential. This analysis should consider not only the initial outlay but also operational savings, lifecycle maintenance costs, and the potential for future scalability.
A seasoned industry consultant noted, Prefab warehouses offer unparalleled flexibility. While the cost might seem significant upfront, the ability to quickly adapt to business growth and changes in market demand can result in substantial long-term financial benefits.
Trustworthiness and Reliability
Choosing a reputable manufacturer with a track record of delivering high-quality prefab warehouses ensures reliability and trustworthiness. Verifying credentials, seeking client testimonials, and reviewing past projects can provide assurance of the manufacturer's capability. Transparent pricing models and a commitment to meeting deadlines are indicative of a reliable partner.
Real-World Experience
Several businesses have shared their experiences with prefab warehouses, highlighting significant cost savings and efficiency gains. For instance, a mid-sized logistics company reported a 20% reduction in construction time and associated costs, enabling them to expand their operations swiftly. Similarly, a manufacturing firm emphasized the ease of integrating advanced technology within their prefab facility, enhancing productivity and sustainability.
Conclusion
Navigating the cost landscape of prefab warehouses requires a nuanced understanding of various influencing factors. By considering design complexities, material choices, logistical aspects, and the long-term benefits, businesses can make informed decisions that align with their strategic goals. As the trend towards prefab warehouses continues to gain momentum, leveraging industry expertise and real-world experiences can ensure a successful investment that meets both current and future needs.