Understanding the Cost Structure of Building a Metal Warehouse
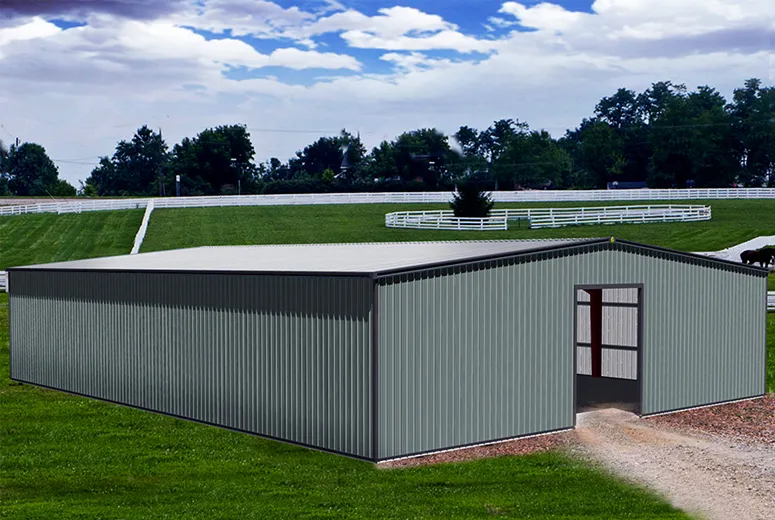
Constructing a metal warehouse is an investment that many businesses consider due to its durability and cost-effectiveness. With increasing competition across industries, understanding the cost structure of building these warehouses is crucial for business owners. Here, we break down the key components that influence these costs to provide a clearer picture.
Material Quality and Type
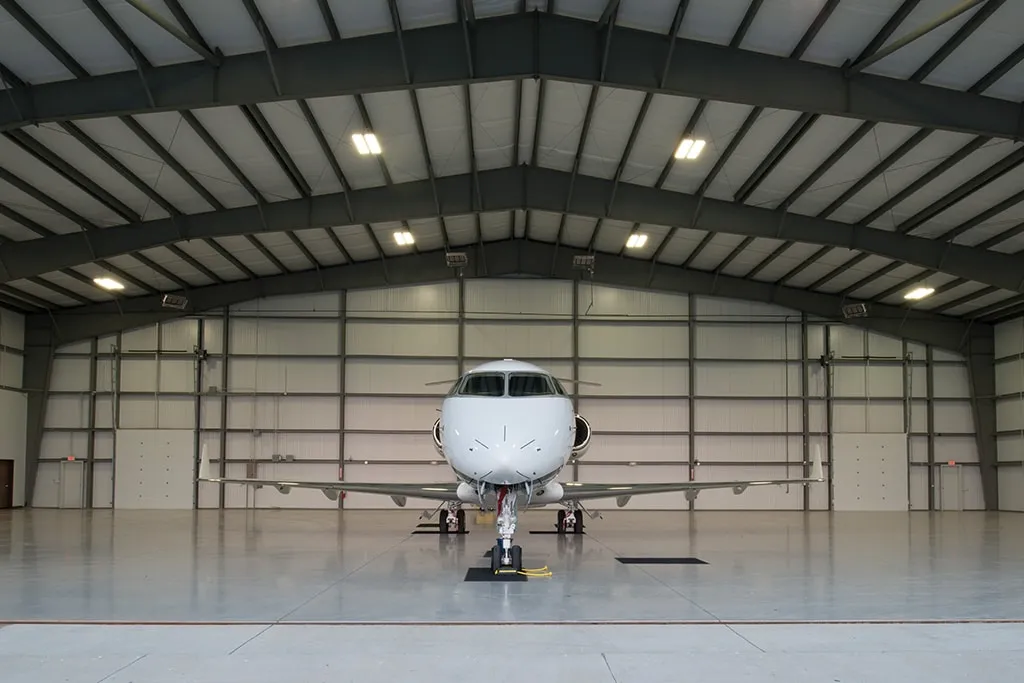
The primary factor affecting the cost of a metal warehouse is the type and quality of materials used. Steel is the most common metal for warehouse construction due to its robustness and longevity. However, the price of steel can fluctuate based on market demand and availability. High-grade steel, which offers better resistance to environmental factors and corrosion, typically comes at a higher price point. Additionally, choosing between galvanized or stainless steel adds another layer of cost variation, as these options provide different levels of durability.
Design and Architecture
Another critical consideration is the design and architectural complexity of the warehouse. A basic structure with minimal customizations will naturally be less expensive. However, incorporating specific design elements such as mezzanine floors, custom shelving, or skylights can significantly increase costs. Engaging with experienced architects who have a background in industrial design is crucial, as they can provide insights on cost-saving opportunities without compromising the warehouse’s functionality or aesthetic appeal.
Construction Labor
The cost of labor is another essential factor. Highly skilled workers are necessary to ensure the integrity and safety of the structure. The geographical location of the warehouse site can influence labor costs due to variations in local wage standards and the availability of skilled workers. Additionally, considerations such as the project's timeline can affect costs, where expedited projects may incur higher labor expenses to meet deadlines.
cost to build a metal warehouse
Site Preparation and Land Costs
Before construction begins, site preparation must be executed, which includes grading, clearing, and ensuring that the site is suitable for construction. These costs can vary widely depending on the site’s existing condition. Additionally, the cost of the land itself is a significant part of the overall budget; prime locations with easy access to transportation hubs or urban centers tend to be more expensive.
Permit and Regulatory Fees
Understanding and navigating local building regulations and permits is crucial to avoid legal and financial setbacks. Permits can incur substantial costs and vary depending on the warehouse size and intended use. It's advisable to work with professionals familiar with local regulations to streamline this process and prevent unnecessary delays.
Continuing Operating Costs
It's essential to consider the long-term operating costs of the warehouse, which include utility expenses, maintenance, and potential upgrades. Metal warehouses are generally low-maintenance, but factors such as insulation and energy-efficient installations should be considered initially to reduce future expenses.
Considering these factors holistically can provide a comprehensive understanding of the costs involved in building a metal warehouse. Companies should approach this investment with careful planning and seek advice from experienced professionals to tailor a solution that fits their financial and operational needs. By thoroughly analyzing these key aspects, businesses can ensure that their investment yields benefits for years to come.